Shrink plastic, also known as shrink film or shrink wrap, is a versatile material used for packaging and other applications. It is made through a process called extrusion.
The first step in making shrink plastic involves melting and mixing together various types of polymer resins, such as polyethylene or polypropylene. These resins are chosen for their ability to shrink when heated.
Once the resins are mixed, they are fed into an extruder machine. The machine heats the resin mixture to a high temperature, causing it to melt into a molten state. The molten plastic is then forced through a die, which shapes it into a continuous sheet or tube.
As the plastic exits the die, it enters a cooling chamber where it solidifies and forms into its desired shape. Depending on the intended application, the plastic may be extruded as a flat sheet or as a tube that can be later cut and sealed.
After cooling and solidifying, the shrink plastic can undergo additional processes such as printing or laminating to enhance its appearance or functionality.
To activate the shrinking properties of the plastic, heat is applied either through hot air or heat tunnels during packaging. As heat is applied, the molecular structure of the plastic relaxes and contracts uniformly around the object being packaged.
The result is a snug and protective covering that conforms tightly to the shape of the item. This helps protect against dust, moisture, and tampering and provides an attractive presentation for retail products.
Overall, shrink plastic is made through an extrusion process that involves melting polymer resins and shaping them into sheets or tubes. Its versatility makes it widely used in various industries for packaging purposes due to its ability to conform tightly around objects when heated.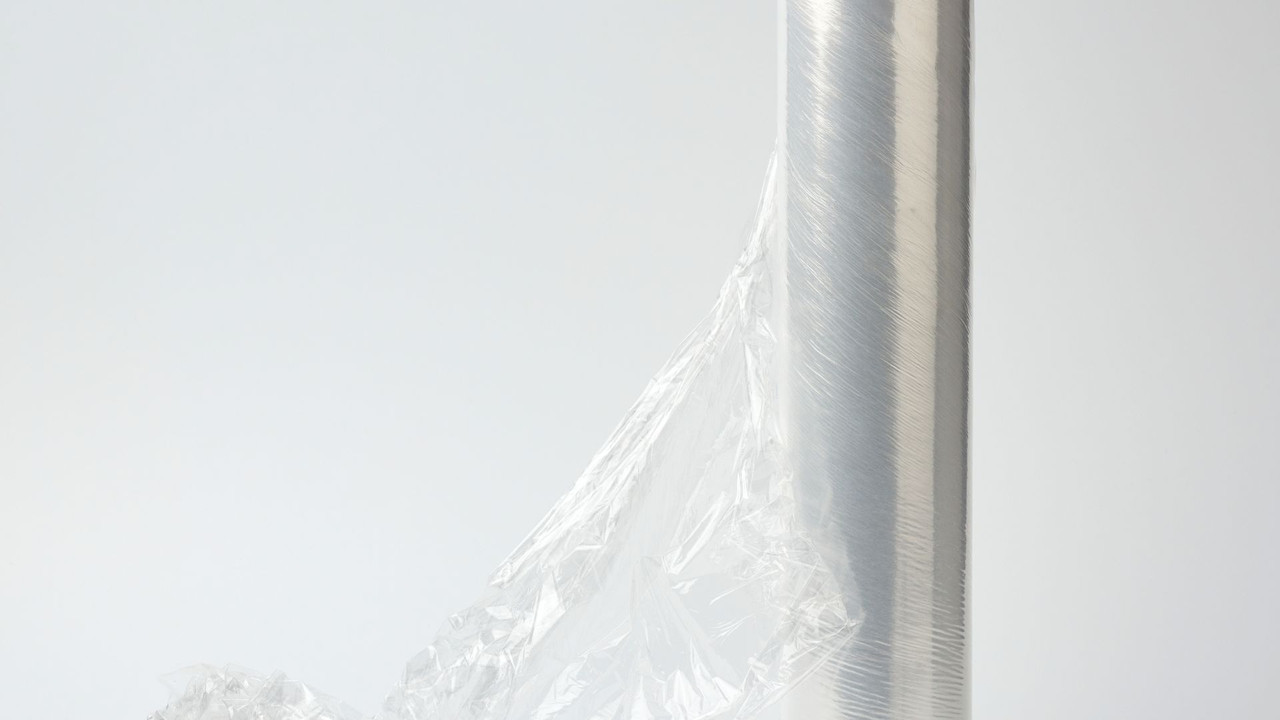